As the world transitions toward low-carbon energy systems, hydrogen has emerged as a cornerstone of decarbonisation strategies. Governments, industries, and technology providers are accelerating the deployment of hydrogen-powered solutions – ranging from mobility applications to large-scale energy storage and industrial processes.
However, enabling the safe, reliable, and efficient use of hydrogen presents unique engineering challenges. One of the most critical yet often overlooked aspects is sealing technology.
Freudenberg Sealing Technologies, a global leader in high-performance sealing solutions, is at the forefront of addressing these challenges. With more than 170 years of materials expertise and a strong commitment to sustainability and innovation, the company provides advanced sealing solutions that support the hydrogen economy across its entire value chain from production and compression to transportation, storage, and end-use applications.
The challenge: Sealing hydrogen in demanding conditions
Hydrogen is the lightest and smallest molecule in the universe. Its unique properties make it an excellent energy carrier but also create complex containment issues.
Due to its low molecular weight, hydrogen can easily permeate many materials, leading to potential leakage. Moreover, hydrogen embrittlement, high diffusion rates, and extreme operating conditions (pressures exceeding 700 bar and temperatures ranging from cryogenic to over 150°C) place extraordinary demands on sealing materials.
These challenges of sealing hydrogen require a fundamentally different approach. Standard elastomers and plastics often fail when exposed to hydrogen, especially under high pressures and dynamic conditions. Freudenberg Sealing Technologies’ answer is to develop materials and designs that ensure long-term durability, safety, and efficiency in these environments.
Material innovations for hydrogen applications
At the core of hydrogen sealing solutions is the proprietary materials portfolio of Freudenberg Sealing Technologies. The company has engineered a range of high-performance elastomers, thermoplastics, and polyurethane materials optimised for hydrogen service.
One standout is the high-resistance hydrogen elastomer family. These materials exhibit exceptional low-temperature flexibility, chemical resistance, and ultra-low permeability. They have been extensively tested for performance in high-pressure hydrogen environments and have shown minimal degradation over time. In addition, they demonstrate high resistance to explosive decompression – a critical factor for seals used in refueling stations, valves, and storage systems.
The company’s portfolio also includes innovative thermoplastics for use in static and dynamic seals. These materials resist hydrogen embrittlement and maintain mechanical strength at extreme temperatures. In cryogenic hydrogen applications, PTFE-based compounds maintain tight seals even at -253°C.
Application-specific sealing solutions
Freudenberg Sealing Technologies has already deployed products in key segments of the hydrogen value chain.
Gaskets and seals for PEM (Proton Exchange Membrane) and alkaline electrolysers withstand aggressive media, including oxygen and caustic solutions, and are designed for long service life, reducing maintenance intervals and increasing electrolyser efficiency.
High-pressure hydrogen in compressors and pumps requires seals that can handle pressures up to 1,000 bar. Freudenberg Sealing Technologies supplies customised piston seals, rod seals, and diaphragms for compressors, that combine low leakage with long-lasting durability.
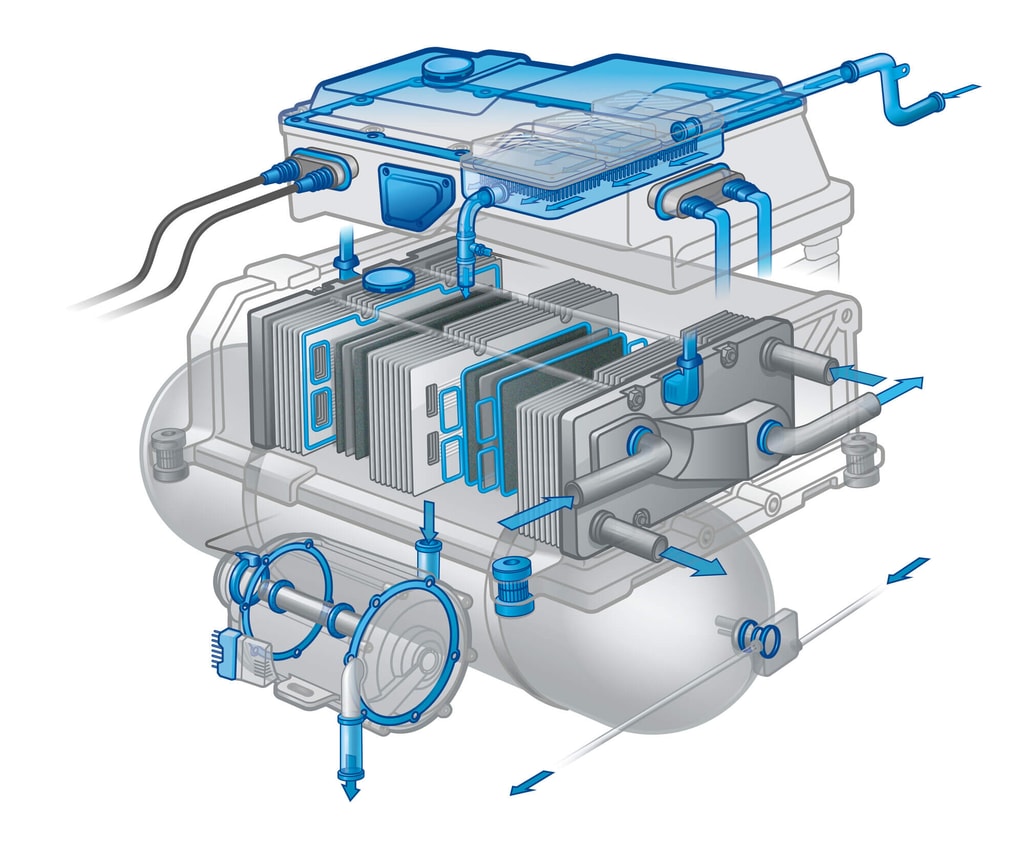
Pressure above 700 bar, cryogenic temperatures, highly dynamic mechanical stress: fuel cell aggregates are a demanding environment for sealings. | ©Freudenberg Sealing Technologies
Hydrogen storage and transportation requires composite storage tanks, pipelines, and distribution systems that rely on seals that prevent leakage and withstand cyclic pressure changes. New sealing systems maintain integrity under fluctuating conditions and comply with international standards such as ISO 14687 and EC79/2009.
For Fuel Cell Vehicles (FCVs), Freudenberg Sealing Technologies supplies specially developed membrane electrode assemblies (MEA) and sealing frames, ensuring robust performance in harsh operating environments. The integrated solutions simplify assembly processes while improving fuel cell efficiency.
Testing and validation: Ensuring safety and reliability
Material development is based on experience, a vast portfolio and rigorous testing to ensure they meet the demanding requirements of hydrogen applications.
This includes permeation testing according to ISO 11114-2, ageing tests, and evaluations under explosive decompression scenarios. Testing is conducted at in-house laboratories and verified by independent third-party institutions.
Supporting the hydrogen economy’s growth
As governments roll out hydrogen strategies and major industries invest in hydrogen infrastructure, Freudenberg Sealing Technologies is working closely with OEMs, system integrators, and energy companies to co-develop new solutions. The companies’ experience in design engineering, simulation, and rapid prototyping enables fast development cycles and tailored solutions for customer-specific applications.
In addition to its technical expertise, Freudenberg Sealing Technologies is committed to sustainability. The company’s hydrogen sealing solutions are designed to extend product life, reduce leakage, and minimise energy loss – contributing to a more sustainable hydrogen economy.
Looking ahead
Hydrogen is no longer a future concept – it is a rapidly growing sector with tangible deployments worldwide. Freudenberg Sealing Technologies plays a vital role in ensuring the safety and efficiency of hydrogen systems, from production to end use.
The company assumes the role of an enabler of the hydrogen economy. The innovative products are helping industries to unlock hydrogen’s potential and drive the transition toward a sustainable, zero-emissions energy future all along the value chain.
A proven supplier
Freudenberg Sealing Technologies is a proven supplier for demanding products and applications, and a development and service partner to customers in the automotive industries and in general industries.
It applies 175 years of engineering and materials expertise. Then and now – the company is focused on serving its customers’ requirements and needs.
Zero defect quality
As a technology expert, Freudenberg Sealing Technologies embraces the ever-increasing demands placed on applications and their materials. Its zero-defect quality compound manufacturing processes enable its innovative solutions to function with reliability.
Selected raw materials, and the company’s own polymers for acrylate and fluorine rubbers, are the ingredients it relies upon to formulate high-quality elastomer compounds. Freudenberg Sealing Technologies uses modern calculation methods and material models to simulate behaviour within the application.